Comprehensive Overview: What is Porosity in Welding and Exactly How to avoid It
Comprehensive Overview: What is Porosity in Welding and Exactly How to avoid It
Blog Article
The Science Behind Porosity: A Comprehensive Guide for Welders and Fabricators
Understanding the intricate devices behind porosity in welding is essential for welders and makers striving for flawless craftsmanship. From the composition of the base products to the complexities of the welding process itself, a plethora of variables conspire to either worsen or alleviate the visibility of porosity.
Comprehending Porosity in Welding
FIRST SENTENCE:
Examination of porosity in welding exposes essential understandings right into the integrity and high quality of the weld joint. Porosity, characterized by the presence of tooth cavities or voids within the weld metal, is a common issue in welding procedures. These voids, if not effectively dealt with, can endanger the structural stability and mechanical residential properties of the weld, leading to prospective failings in the completed product.

To discover and measure porosity, non-destructive screening approaches such as ultrasonic screening or X-ray inspection are typically utilized. These strategies permit for the recognition of internal defects without jeopardizing the stability of the weld. By examining the dimension, form, and circulation of porosity within a weld, welders can make informed choices to enhance their welding procedures and accomplish sounder weld joints.
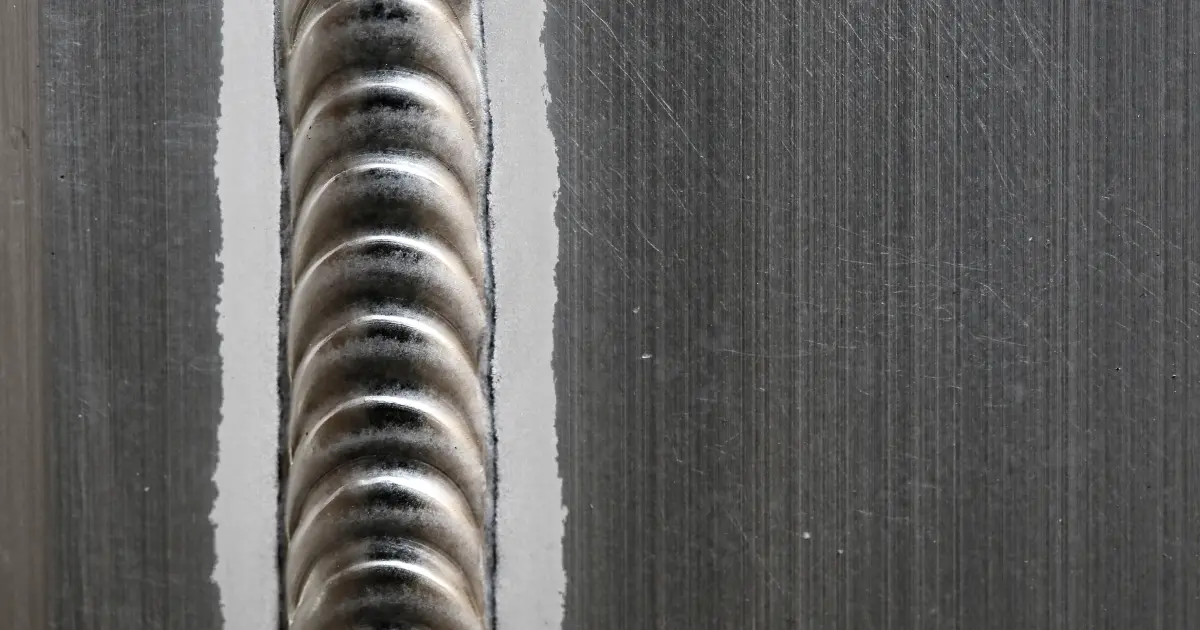
Factors Influencing Porosity Formation
The incident of porosity in welding is affected by a myriad of elements, ranging from gas protecting effectiveness to the details of welding parameter setups. Welding parameters, consisting of voltage, existing, take a trip speed, and electrode kind, also influence porosity development. The welding technique used, such as gas metal arc welding (GMAW) or protected steel arc welding (SMAW), can influence porosity development due to variants in heat circulation and gas coverage - What is Porosity.
Impacts of Porosity on Weld Top Quality
The visibility of porosity additionally damages the weld's resistance to corrosion, as the trapped air or gases within the gaps can respond with the surrounding setting, leading to deterioration over time. Furthermore, porosity can hinder the weld's capacity to stand up to pressure or effect, additional jeopardizing the total top quality and dependability of the welded framework. In important applications such as aerospace, vehicle, or architectural buildings, where safety and resilience are paramount, the destructive results of porosity on weld high quality can have extreme effects, highlighting the importance of decreasing porosity with proper welding strategies and procedures.
Methods to Lessen Porosity
To enhance the top quality of bonded joints and ensure architectural stability, welders and makers utilize particular strategies aimed at reducing the development of voids and tooth cavities within the product during the welding procedure. One effective approach to minimize porosity is to make sure proper material preparation. This includes detailed cleaning of the base metal to get rid of any impurities such as oil, grease, or wetness that can add to porosity formation. In look at this site addition, using the proper welding criteria, such as the appropriate voltage, existing, and travel rate, is vital in avoiding porosity. Maintaining a regular arc length and angle during welding check my site additionally helps decrease the probability of porosity.

Using the appropriate welding strategy, such as back-stepping or utilizing a weaving activity, can additionally assist distribute warmth equally and minimize the chances of porosity development. By carrying out these techniques, welders can properly lessen porosity and produce top notch welded joints.

Advanced Solutions for Porosity Control
Implementing innovative technologies and ingenious approaches plays a pivotal role in achieving superior control over porosity in welding procedures. In addition, employing innovative welding methods such as pulsed MIG welding or modified ambience welding can additionally help reduce porosity problems.
Another sophisticated remedy includes using innovative welding devices. As an example, utilizing devices with integrated attributes like waveform control and innovative source of power can enhance weld top quality and reduce porosity risks. Furthermore, the implementation of automated welding systems with precise control over parameters can considerably reduce porosity issues.
In addition, including innovative monitoring and evaluation technologies such as real-time X-ray imaging or automated ultrasonic testing can help in discovering porosity early in the welding procedure, permitting instant rehabilitative activities. Generally, incorporating these sophisticated services can significantly improve porosity control and i was reading this enhance the total top quality of bonded components.
Conclusion
In verdict, recognizing the science behind porosity in welding is crucial for welders and producers to generate premium welds - What is Porosity. Advanced solutions for porosity control can additionally enhance the welding procedure and ensure a strong and trusted weld.
Report this page